With the arrival of warm weather, our minds turn to sunny days, beach trips, and outdoor adventures. However, amidst the joy of summer, a silent threat looms: corrosion. While many associate it with winter weather, corrosion can impact vehicles, appliances, industrial equipment, and metal structures year-round. Understanding the causes, effects, and prevention measures related to summer corrosion is essential, and selecting a low-carbon footprint solution is paramount to protecting our surfaces and our environment.
Causes of Summer Corrosion
Summer weather brings a number of known and hidden corrosion risks. Salt exposure, for example, is not just a consequence of winter road treatments. Our coastal regions expose all types of surfaces to salt, humidity, and temperature swings. However, salt is just one of the risk factors associated with summer weather conditions. The rate of corrosion increases substantially with temperature, meaning the risk of corrosion increases as the summer months progress. High temperatures, combined with increased humidity, accelerate
corrosion on metal surfaces. UV radiation from sunlight can break down protective coatings, leaving surface finishes more vulnerable to rust, discoloration, and deterioration.
With summer also comes temperature fluctuations. From warm days to cool evenings, surfaces are exposed to temperature swings which cause them to expand and contract. This movement can create cracks, chips, or wear, compromising the integrity of finished surfaces.
These risk factors are further exacerbated in urban and industrial areas where buildings and equipment are exposed to increased pollution levels. Pollutants like sulfur dioxide and nitrogen oxides react with moisture during hot, humid months, forming acidic compounds commonly referred to as acid rain, which attack surfaces unrelentingly.
Human factors also contribute to increased corrosion in the summer months. Perspiration, sunscreens, oils, and makeup can cause corrosion in the form of stains on interior and exterior vehicle surfaces. Automotive manufacturers understand this, with many OEMs creating performance test standards to grade performance against contact corrosion caused by these accelerants. Similar risks impact surfaces within homes and buildings, from faucets to handles, where sunscreen, lotions, and body oil can leave unwanted stains and marks.
Effects of Summer Corrosion
Corrosion can impact the strength, performance, and visual appeal of metal surfaces. From the decorative and functional parts of our vehicles to the metal components supporting buildings and industrial equipment, corrosion can leave lasting, and irreversible effects. The weakening of these foundational materials can compromise the safety and longevity of buildings, bridges, and infrastructure. Recently, the impact of oxidation has been seen on wind turbines and solar panels exposed to extreme climate conditions as these sustainable energy sources proliferate.
Along with structural integrity, corrosion can cause equipment, machinery, and vehicle failures. Whether caused by road salts or heat and humidity, electrical connections, moving parts, and critical components are all at risk. This can affect everything from braking and suspension systems in a vehicle to the controls within large industrial equipment, and the result of these failures can be costly and dangerous.
Summer corrosion can also be an unwanted headache, impacting the aesthetic and appearance of homes, office buildings, and vehicles. Corroded metal surfaces detract from the overall appearance of structures, architectural elements, and decorative finishes, while blemishes on surfaces caused by summer perspiration and creams can be unsightly.
Whether causing critical damage and decay, or an unappealing stain on a vehicle’s interior, the effects of corrosion throughout the summer season are a cause for concern that can and should be avoided through the proper selection of surface finishes.
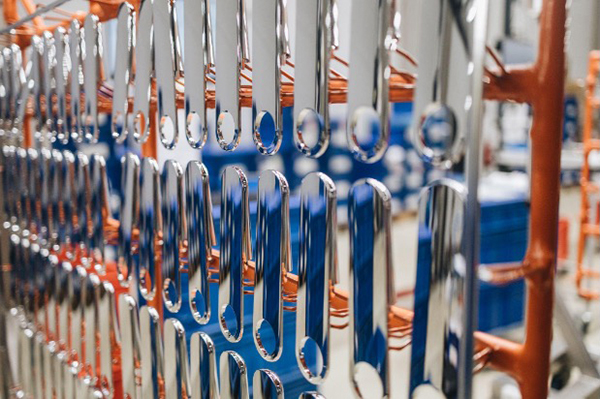
Preventing Summer Corrosion
Surface finishing solutions are available across industries and applications to protect surfaces and combat corrosion. From multi-layer decorative finishes to sacrificial functional finishes, these solutions address the common causes of oxidation on vehicles, buildings, equipment, and infrastructure.
Multi-layer coatings are designed to protect vehicles against expansion and contraction, extreme heat, and UV radiation. These stacked finishes absorb thermal movement experienced on the surface of vehicle trim and equipment, reducing the risk of degradation on the protective layers. Specifically engineered metal layers serve as a final finish to ensure functional performance while also protecting the surface color and appearance from blemishes, fading, and wear. Selecting the correct layers and thickness for each application is critical for producing the desired performance.
The aluminum surfaces on window treatments, solar panels, and building facades also require anodizing and passivation to protect them from environmental conditions, acid rain in urban areas, and oxidation which can compromise the integrity of the base metal. The use of aluminum continues to rise dramatically for its light weight and recyclability, making these surface finishes an important technology selection.
Interior surfaces of vehicles and buildings, including decorative automotive finishes, housing fixtures, appliances, and sanitary fittings, require protection against contact corrosion. Specific surface treatment technologies are applied to extend the life of these surfaces, with protection against scratches, stains, blemishes, and chips.
Sustainable Protection
Summer corrosion protection should not come at the expense of the environment. Inherently, metal plating has a smaller carbon footprint when compared to alternative coatings. These coatings, which are designed to protect surfaces, are developed with sustainability at the forefront, removing substances of very high concern, including PFAS, from their processes. Conscientious manufacturers remain committed to continuous innovation and are adopting anti-corrosion and decorative finishing solutions that reduce environmental footprint while optimizing performance.
Whether for vehicles and equipment, or wind turbines, solar panels, and architectural elements, the right surface treatment can significantly extend the lifespan of metal surfaces. To select the appropriate finish, manufacturers should consider summer corrosion and partner with the right supplier to deliver tailored sustainable finishing solutions that drive high performance. By implementing effective prevention measures, we can protect valuable assets and maintain their functionality and appearance for years to come, while decreasing our carbon footprint.
Check out the full article, available now on industrytoday.com